Above photo by Brian Quarstad
If you’ve spent any time on 94 driving between the Twin Cities recently, it’s hard to miss the developments at Allianz Field that are beginning to give a clear view of what Minnesota United’s soccer-specific stadium is going to look like when completed. Recently, Mortenson began installing the PTFE screen that will give Allianz Field its signature look and with the fifth of 10 panels going up on Wednesday, that process is about half done. The goal is for the membrane to mimic the qualities of water in Minnesota’s lakes — sparkling and bright in the sun yet transparent and refractive in the shade. We sat down with Construction Executive Greg Huber and Project Engineer Nate Weingart of Mortenson to learn more.
What exactly is the PTFE screen made of and how is it created?
Weingart: The material is a fiberglass weave that is laminated with PTFE [or polytetrafluoroethylene, the basis of Teflon]. So PTFE is actually a polymer and kind of a plastic. That is the material that is used to laminate this fiberglass weave that creates the membrane system. It is basically a fiberglass weave that is pigmented silver and then laminated with a PTFE polymer material.
Think of it as a quilt. The material of the quilt is made in Merrimack, New Hampshire. It is a big roll of material that is then sent over to Shanghai. Shanghai maps out in a computer program how these big rolls will be cut into smaller squares for the quilt. They call them templates. Then they have this automated cutting machine that takes a roll and cuts all these little pieces out from a big roll and then they take those pieces and lay them out on a shop floor. Using hand irons and welding machines, they use heat and pressure to weld all of these patches into the larger quilt that ends up being the panel.
Then they fold up a 10,000-square-foot panel into a 10-foot by five-foot by eight-foot crate using foam noodles. It is a pretty fragile material, just because there is glass yarn on them and you don’t want those breaking. So they use foam noodles and everything they can to fold it up nicely and securely and put it into a crate and ship it back to the United States where we receive it on site.
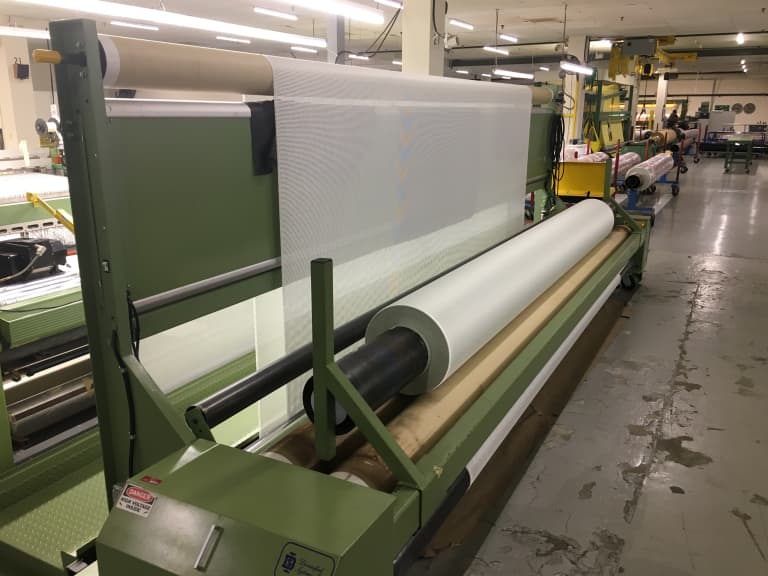
You mentioned that it’s fragile when it’s being folded and shipped, but how durable is it once it’s installed?
Huber: Once it is installed and tensioned, it is an extremely strong material. It is the first time this material has ever been used, so it is a very cutting edge material. The reason the whole material was created in the first place was for superior structural durability and tear resistance. This material is a very durable, heavy-duty material that still has those translucent properties that makes it architectural. That was the big feat in this whole material engineering: to have a super durable material that is structurally capable of spanning large distances, while still remaining translucent.
In the past these materials have not been able to be tinted with color or been able to be translucent. That is the whole key. It doesn’t let wind through or water through. That’s a really important element for fan comfort because it will protect from the winds during the shoulder seasons of the season. It wraps around the entire stadium, so you don’t have the giant winds that will come in and kill you. It is a rain screen, so basically rain bounces off of it.
This being Minnesota, cold and snow are obviously a big concern for any building project. How does the PTFE screen stand up to those kind of elements?
Huber: It is just used on the vertical elements, so it is not used on the roof. So there is very little snow load like the Metrodome had.
As far as the cold weather goes, we have tested it and understood the thermal properties of it. It can handle the Minnesota temperature swing. It will actually contract a little bit more than the steel will. Once it gets down to 10 or 20 below, it actually becomes tighter than the steel. The membrane gets tighter, which is a pretty key element for us.
Tell us a little bit about what goes into actually getting the panels onto the building.
Weingart: The white steel that you see out there right now has connection points that receive a base aluminum material. There is a base aluminum bar that is installed on the white steel and that serves as the base for the fabric to sit on.
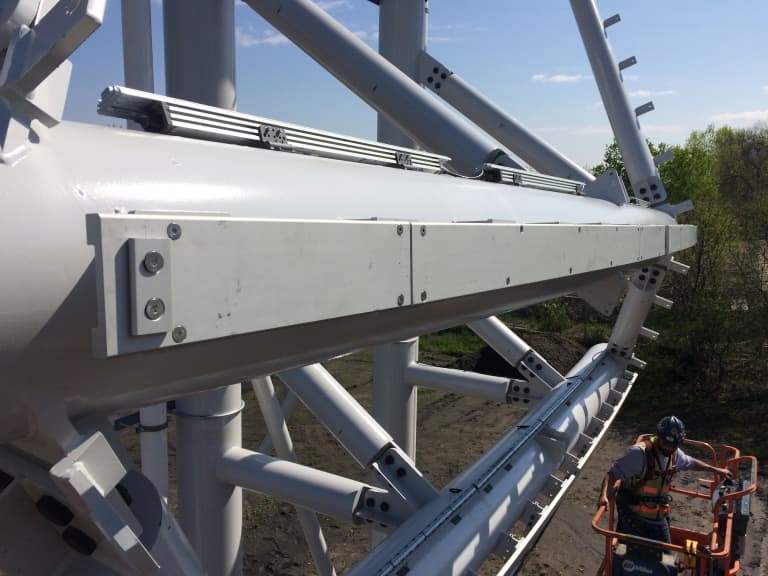
So all of that aluminum is installed in an area and then the panel that is associated with that area is unfolded on the ground and rigged up using pulleys at the very top and winches on the very bottom. On our largest panel we had about 10 winches set up across the area. One by one you go across and you pull each winch up. You kind of work the panel from left to right, pulling it up one or two feet at a time, and then you work your way back from right to left. You keep doing that until you get the panel up in the air and up to where you want it and then they hook up the connections on the top steel member and start with the top and then work and connect the sides. They connect the perimeter of the panel first once they have it up in position and once they then have it connected all the way around then they start pulling it tight. [The tension] is about 25 pounds per lineal inch in each direction. When you do the “tap test,” you flick it with your finger, it sounds like a drum you’d play in a high school band. It is pretty tight.
Once the PTFE panels are in place, the lighting system that will illuminate them in any color of the rainbow — red, white and blue for July 4 or purple for Prince's birthday or a flowing combination of greens to evoke the northern lights — will get a comprehensive test. But more on that later.